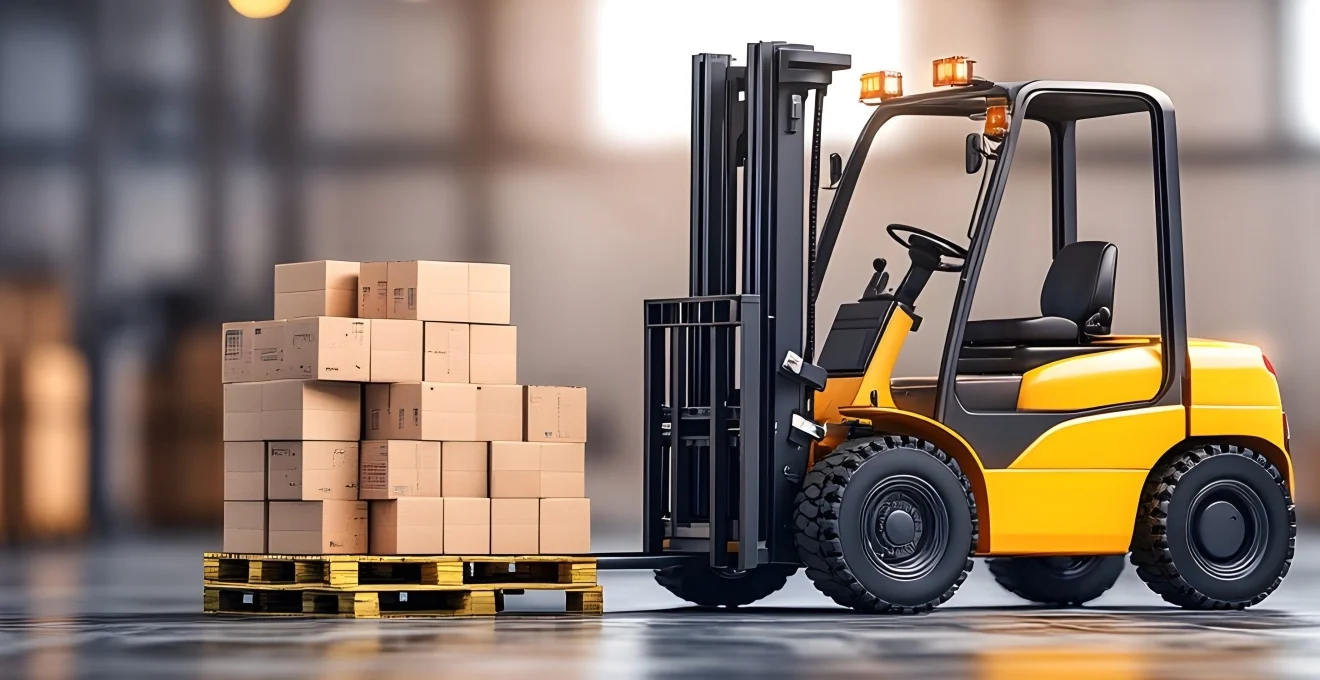
Dans le monde industriel en constante évolution, le choix du bon matériel de manutentionest devenu un élément clé pour assurer la sécurité des travailleurs et optimiser la productivité. Que ce soit dans les entrepôts logistiques, les usines de production ou les zones portuaires, l'utilisation d'équipements adaptés permet non seulement de faciliter le déplacement des marchandises, mais aussi de réduire les risques d'accidents et d'améliorer l'efficacité opérationnelle. Face à la diversité des environnements de travail et des besoins spécifiques de chaque industrie, il est crucial de comprendre les différents types de matériel disponibles, les normes en vigueur et les innovations technologiques qui façonnent ce secteur en pleine mutation.
Types de matériel de manutention adaptés aux différents environnements de travail
Le choix du matériel de manutention dépend grandement de l'environnement de travail et des tâches à accomplir. Chaque type d'équipement présente des caractéristiques uniques qui le rendent particulièrement adapté à certaines situations. Examinons en détail les principaux types de matériel utilisés dans différents contextes industriels.
Chariots élévateurs et transpalettes pour entrepôts logistiques
Dans les entrepôts logistiques, les chariots élévateurs et les transpalettes sont des outils indispensables. Les chariots élévateurs, disponibles en versions thermiques ou électriques, permettent de soulever et déplacer des charges lourdes sur de courtes distances. Leur polyvalence les rend particulièrement utiles pour le chargement et déchargement de camions, ainsi que pour le stockage en hauteur. Les transpalettes, quant à eux, sont idéaux pour le déplacement de palettes sur des surfaces planes. Leur compacité et leur maniabilité en font des outils de choix pour naviguer dans les allées étroites des entrepôts.
Il est important de noter que le choix entre un chariot élévateur électrique ou thermique dépend de plusieurs facteurs, notamment la durée d'utilisation quotidienne, l'environnement de travail (intérieur ou extérieur) et les contraintes en termes d'émissions polluantes. Les modèles électriques sont de plus en plus privilégiés pour leur faible impact environnemental et leur silence de fonctionnement, particulièrement appréciés dans les espaces clos.
Ponts roulants et palans pour industries lourdes
Dans les industries lourdes telles que la métallurgie ou la construction navale, les ponts roulants et les palans jouent un rôle crucial. Ces équipements permettent de déplacer des charges extrêmement lourdes avec précision, tout en optimisant l'utilisation de l'espace vertical des ateliers. Les ponts roulants, installés en hauteur, peuvent traverser toute la largeur d'un bâtiment, offrant ainsi une grande flexibilité dans la manutention de pièces volumineuses.
Les palans, souvent utilisés en complément des ponts roulants ou de façon indépendante, offrent une solution de levage ponctuelle et précise. Leur capacité de levage peut varier de quelques centaines de kilos à plusieurs tonnes, s'adaptant ainsi à une grande variété de besoins industriels. L'utilisation de ces équipements nécessite une formation spécifique et une attention particulière aux règles de sécurité, compte tenu des risques liés à la manipulation de charges lourdes en hauteur.
Convoyeurs et systèmes automatisés pour chaînes de production
Les chaînes de production modernes s'appuient largement sur les convoyeurs et les systèmes automatisés pour optimiser leurs flux de matériaux et de produits. Ces équipements permettent un transport continu et fluide des marchandises, réduisant ainsi les temps de manutention et les risques d'erreurs humaines. Les convoyeurs peuvent être conçus sur mesure pour s'adapter parfaitement à la configuration de l'usine et aux spécificités des produits transportés.
Les systèmes automatisés, tels que les AGV (Automated Guided Vehicles) ou les robots de palettisation, représentent l'avenir de la manutention industrielle. Ces technologies permettent non seulement d'augmenter la productivité, mais aussi d'améliorer la traçabilité des produits tout au long de la chaîne de production. L'intégration de ces systèmes nécessite une planification minutieuse et une réflexion approfondie sur l'organisation du travail, mais les bénéfices en termes d'efficacité et de réduction des coûts à long terme sont considérables.
Équipements spécialisés pour manutention portuaire et aéroportuaire
Les zones portuaires et aéroportuaires présentent des défis uniques en matière de manutention, nécessitant des équipements hautement spécialisés. Dans les ports, on trouve des portiques de quai capables de charger et décharger rapidement les porte-conteneurs, ainsi que des chariots cavaliers pour le transport des conteneurs sur les terminaux. Ces équipements doivent être conçus pour résister aux conditions maritimes et supporter des charges extrêmement lourdes.
Dans les aéroports, les équipements de manutention doivent allier rapidité, précision et respect des normes de sécurité aéronautiques. On y trouve des loaders pour le chargement des soutes d'avion, des tracteurs de piste pour le déplacement des avions au sol, et des tapis bagages automatisés pour le tri et l'acheminement des bagages. La fiabilité de ces équipements est cruciale pour assurer la ponctualité des vols et la satisfaction des passagers.
L'investissement dans du matériel de manutention adapté n'est pas simplement une question de productivité, c'est avant tout un engagement envers la sécurité et le bien-être des travailleurs.
Normes et réglementations en vigueur pour le matériel de manutention
La sécurité est au cœur des préoccupations dans le domaine de la manutention industrielle. Pour garantir la protection des opérateurs et la fiabilité des équipements, de nombreuses normes et réglementations ont été mises en place au niveau européen et national. Ces règles strictes encadrent la conception, la fabrication et l'utilisation du matériel de manutention.
Directive machines 2006/42/CE et marquage CE
La Directive Machines 2006/42/CE est le texte de référence au niveau européen pour tout ce qui concerne la sécurité des machines, y compris le matériel de manutention. Cette directive définit les exigences essentielles de santé et de sécurité auxquelles doivent répondre les équipements avant leur mise sur le marché. Le marquage CE, apposé sur les machines conformes, atteste du respect de ces exigences.
Pour obtenir le marquage CE, les fabricants doivent suivre un processus rigoureux d'évaluation des risques et de conformité. Cela implique souvent des tests approfondis et la production d'une documentation technique détaillée. Il est important de noter que le marquage CE n'est pas une simple formalité administrative, mais bien une garantie de sécurité pour les utilisateurs.
Normes ISO 3691 pour la sécurité des chariots de manutention
La série de normes ISO 3691 concerne spécifiquement la sécurité des chariots de manutention. Ces normes internationales définissent les exigences techniques et les méthodes d'essai pour différents types de chariots, qu'ils soient à conducteur porté, à conducteur accompagnant ou automatisés. Elles couvrent des aspects tels que la stabilité, les systèmes de freinage, la visibilité et les dispositifs de protection.
L'application de ces normes permet d'assurer un niveau de sécurité élevé et uniforme à l'échelle mondiale. Pour les entreprises, le respect de ces normes est non seulement une obligation légale, mais aussi un gage de qualité et de fiabilité pour leurs équipements de manutention.
Réglementation INRS ED 6067 sur la prévention des risques
En France, l'INRS (Institut National de Recherche et de Sécurité) a publié le guide ED 6067, qui traite spécifiquement de la prévention des risques liés à l'utilisation des équipements de travail mobiles. Ce document fournit des recommandations précieuses pour l'évaluation des risques, le choix des équipements adaptés et la formation des opérateurs.
Le guide ED 6067 met l'accent sur l'importance d'une approche globale de la sécurité, intégrant à la fois les aspects techniques des équipements et les facteurs organisationnels et humains. Il aborde des sujets tels que l'aménagement des zones de circulation, la signalisation, et les procédures de travail sécuritaires.
La conformité aux normes et réglementations n'est pas une contrainte, mais un investissement dans la sécurité et la performance à long terme de l'entreprise.
Maintenance préventive et entretien du matériel de manutention
La maintenance préventive et l'entretien régulier du matériel de manutention sont essentiels pour garantir sa longévité, sa fiabilité et la sécurité des opérateurs. Une stratégie de maintenance bien planifiée permet non seulement de prévenir les pannes coûteuses, mais aussi d'optimiser les performances des équipements tout au long de leur cycle de vie.
Protocoles d'inspection quotidienne des équipements
L'inspection quotidienne des équipements de manutention est la première ligne de défense contre les défaillances et les accidents. Ces contrôles, effectués par les opérateurs avant chaque utilisation, permettent de détecter rapidement les anomalies et de prévenir les problèmes potentiels. Un protocole d'inspection typique peut inclure :
- Vérification des niveaux de fluides (huile, carburant, liquide de refroidissement)
- Contrôle de l'état des pneus et de la pression
- Test des systèmes de freinage et de direction
- Inspection visuelle des fourches, chaînes et autres éléments critiques
- Vérification du bon fonctionnement des dispositifs de sécurité
Il est crucial de former les opérateurs à ces inspections et de leur fournir des check-lists standardisées pour s'assurer que tous les points importants sont systématiquement vérifiés. Toute anomalie détectée doit être immédiatement signalée et l'équipement ne doit pas être utilisé jusqu'à ce que le problème soit résolu.
Planification des révisions périodiques selon les préconisations constructeurs
Au-delà des inspections quotidiennes, les équipements de manutention nécessitent des révisions périodiques plus approfondies, conformément aux recommandations des fabricants. Ces interventions, généralement planifiées en fonction du nombre d'heures d'utilisation ou à intervalles réguliers, permettent de maintenir les performances des équipements et de prévenir les pannes majeures.
Un plan de maintenance typique peut inclure :
- Changement des fluides et filtres
- Inspection et ajustement des systèmes mécaniques
- Contrôle et remplacement si nécessaire des pièces d'usure
- Vérification et calibrage des systèmes électroniques
- Test complet des fonctions de sécurité
Il est recommandé de tenir un registre détaillé de toutes les interventions de maintenance pour chaque équipement. Ces données sont précieuses pour suivre l'historique des machines, anticiper les besoins futurs et optimiser les coûts de maintenance à long terme.
Gestion informatisée de la maintenance avec logiciels GMAO
La gestion de la maintenance assistée par ordinateur (GMAO) est devenue un outil indispensable pour les entreprises disposant d'un parc important d'équipements de manutention. Ces logiciels permettent de centraliser toutes les informations relatives à la maintenance, de planifier les interventions et de suivre les coûts associés.
Les avantages d'un système GMAO incluent :
- Planification automatisée des interventions de maintenance
- Suivi en temps réel de l'état des équipements
- Gestion des stocks de pièces détachées
- Analyse des données pour optimiser les stratégies de maintenance
- Génération de rapports détaillés pour la prise de décision
L'utilisation d'un logiciel GMAO permet non seulement d'améliorer l'efficacité de la maintenance, mais aussi de réduire les temps d'arrêt des équipements et d'optimiser les coûts opérationnels. C'est un investissement qui se rentabilise rapidement pour les entreprises soucieuses de maximiser la disponibilité et la fiabilité de leur matériel de manutention.
Formation et habilitation des opérateurs de matériel de manutention
La formation et l'habilitation des opérateurs sont des éléments cruciaux pour garantir une utilisation sûre et efficace du matériel de manutention. Au-delà du simple respect des obligations légales, une formation de qualité contribue à réduire les accidents, à améliorer la productivité et à prolonger la durée de vie des équipements.
CACES R389 pour la conduite des chariots automoteurs
Le Certificat d'Aptitude à la Conduite En Sécurité (CACES) R389 est la référence en matière de formation à la conduite des chariots automoteurs de manutention à conducteur porté. Cette certification, bien que non obligatoire légalement, est largement reconnue et exigée par de nombreux employeurs. Elle couvre différentes catégories de chariots, chacune correspondant à des types d'équipements spécifiques.
La formation CACES R389 comprend généralement :
- Une formation théorique sur la réglementation et les principes de sécurité
- Des exercices pratiques de conduite et de manœuvres
- Une évaluation théorique et pratique des compétences
La validité du CACES R389 est généralement de 5 ans, après quoi un recyclage est nécessaire pour maintenir la certification. Il est important de noter que le CACES ne remplace pas l'autorisation de conduite délivrée par l'employeur, mais en constitue un prérequis recommandé.
Autorisation de conduite délivrée par l'employeur
L'autorisation de conduite est un document obligatoire, délivré par l'employeur, qui atteste de la capacité d'un opérateur à conduire un équipement de manutention spécifique en toute sécurité. Cette autorisation est basée sur trois éléments essentiels :
- Un examen d'aptitude médicale réalisé par le médecin du travail
- Une vérification des connaissances et du savoir-faire de l'opérateur pour la conduite en sécurité
- Une connaissance des lieux et des instructions à respecter sur le site d'utilisation
L'employeur doit s'assurer que ces trois conditions sont remplies avant de délivrer l'autorisation de conduite. Il est également responsable de son renouvellement périodique et de sa mise à jour en cas de changement d'équipement ou de conditions de travail.
Formations spécifiques aux équipements complexes
Pour les équipements de manutention plus complexes, tels que les portiques ou les grues, des formations spécifiques sont nécessaires. Ces formations vont au-delà du CACES standard et abordent les particularités techniques et les risques spécifiques liés à ces machines.
Ces formations spécialisées peuvent inclure :
- L'étude approfondie de la structure et du fonctionnement de l'équipement
- Les techniques de levage et de manutention spécifiques
- La gestion des situations d'urgence et des conditions météorologiques extrêmes
- La communication et la coordination avec les équipes au sol
Ces formations sont souvent dispensées par des organismes spécialisés ou directement par les fabricants des équipements. Elles sont essentielles pour garantir une utilisation sûre et efficace de ces machines complexes, qui présentent des risques élevés en cas de mauvaise manipulation.
Innovations technologiques dans le matériel de manutention
Le secteur de la manutention connaît une révolution technologique qui transforme radicalement les équipements et les pratiques. Ces innovations visent à améliorer la sécurité, l'efficacité et la durabilité des opérations de manutention.
Systèmes de guidage laser pour chariots automatisés AGV
Les chariots automatisés guidés (AGV) équipés de systèmes de guidage laser représentent une avancée majeure dans l'automatisation des entrepôts et des usines. Ces systèmes utilisent des lasers pour scanner l'environnement et naviguer avec précision, évitant les obstacles et suivant des trajets prédéfinis.
Les avantages de cette technologie incluent :
- Une précision accrue dans le positionnement et les mouvements
- Une flexibilité permettant de modifier facilement les trajets
- Une réduction des risques d'accidents et de dommages aux marchandises
- Une optimisation de l'utilisation de l'espace dans les entrepôts
Les AGV guidés par laser sont particulièrement adaptés aux environnements dynamiques où les configurations de stockage changent fréquemment. Ils contribuent à augmenter la productivité tout en réduisant les coûts de main-d'œuvre et les erreurs humaines.
Intégration de l'IoT pour la maintenance prédictive
L'Internet des Objets (IoT) révolutionne la maintenance des équipements de manutention en permettant une approche prédictive. Des capteurs intégrés aux machines collectent en temps réel des données sur leur état de fonctionnement, leur utilisation et leurs performances.
Cette technologie offre plusieurs avantages :
- Détection précoce des anomalies et prévention des pannes
- Optimisation des plannings de maintenance
- Réduction des temps d'arrêt imprévus
- Prolongation de la durée de vie des équipements
- Amélioration de la sécurité grâce à une meilleure fiabilité des machines
L'analyse des données collectées permet aux gestionnaires de flotte de prendre des décisions éclairées sur la maintenance et le remplacement des équipements, contribuant ainsi à réduire les coûts opérationnels à long terme.
Équipements électriques et hybrides pour réduire l'empreinte carbone
Face aux préoccupations environnementales croissantes, l'industrie de la manutention se tourne de plus en plus vers des solutions électriques et hybrides. Ces équipements offrent une alternative plus écologique aux moteurs thermiques traditionnels, tout en maintenant des performances élevées.
Les avantages des équipements électriques et hybrides incluent :
- Réduction significative des émissions de CO2 et de particules fines
- Diminution de la pollution sonore, particulièrement appréciable en milieu urbain
- Coûts d'exploitation réduits grâce à une consommation d'énergie optimisée
- Maintenance simplifiée par rapport aux moteurs thermiques
Les progrès dans la technologie des batteries, notamment l'augmentation de leur capacité et la réduction des temps de charge, rendent ces solutions de plus en plus viables pour une utilisation intensive. De nombreuses entreprises adoptent ces technologies pour réduire leur empreinte carbone et se conformer aux réglementations environnementales de plus en plus strictes.
L'innovation dans le matériel de manutention ne se limite pas à l'amélioration des performances techniques ; elle vise également à créer un environnement de travail plus sûr, plus efficace et plus respectueux de l'environnement.